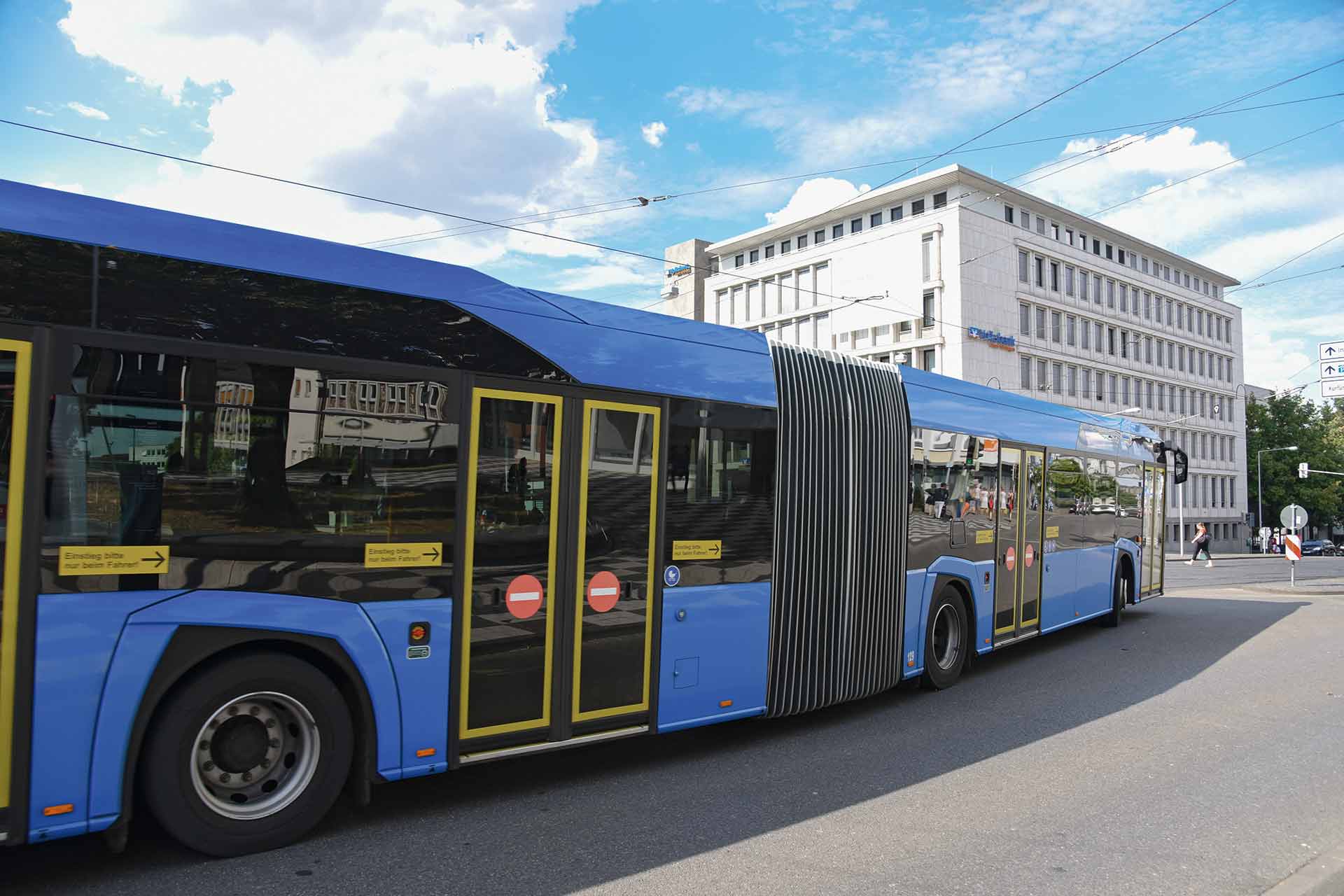
Produkte und Konzepte
für Busse

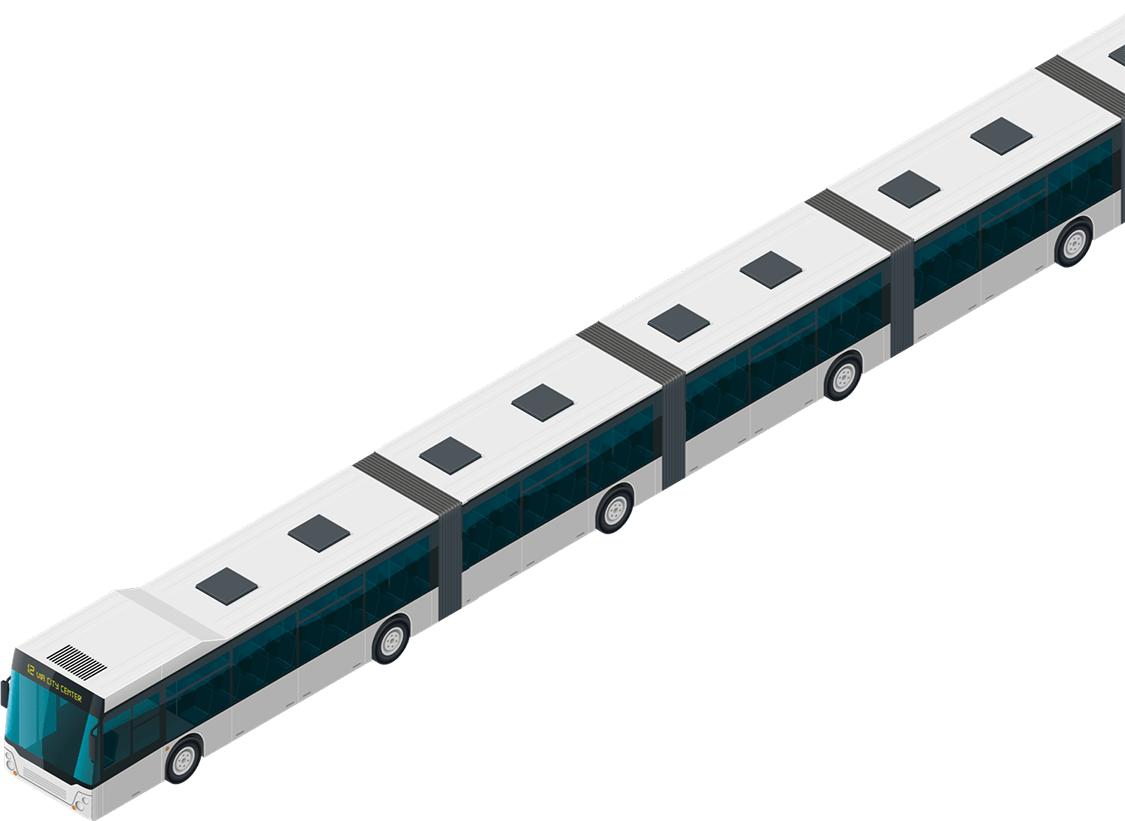
Wir bauen 1,60 m Bus
Ohne HÜBNER würde Gelenkbussen etwas fehlen – und zwar mindestens 1,60 Meter. Gespickt mit modernster Technik. HÜBNER liefert einbaufertige Komplettsysteme für alle Arten von Gelenk- und Doppelgelenkbussen in Niederflur- oder Hochflurausführung. Darin enthalten sind Gelenksystem, Faltenbalg, Energieführung, elektronische Gelenksteuerung und Teile der Innenraumgestaltung.
Unser 1,60 m Bus ist ein komplett einbaufertiges Plug-and-Play-System zur Verbindung des hinteren Teils eines Gelenkbusses mit dem vorderen Teil. Ausgeliefert wird das Komplettsystem auf Ladungsträgern, damit es innerhalb weniger Stunden in den Bus montiert werden kann.
Ihr Kontakt
Christian Arndt
Vertriebsleiter Straße
Tel. +49 561 998 1732
christian.arndt(@)hubner-group.com
Entdecken Sie unsere vielfältige Produktpalette für Busse
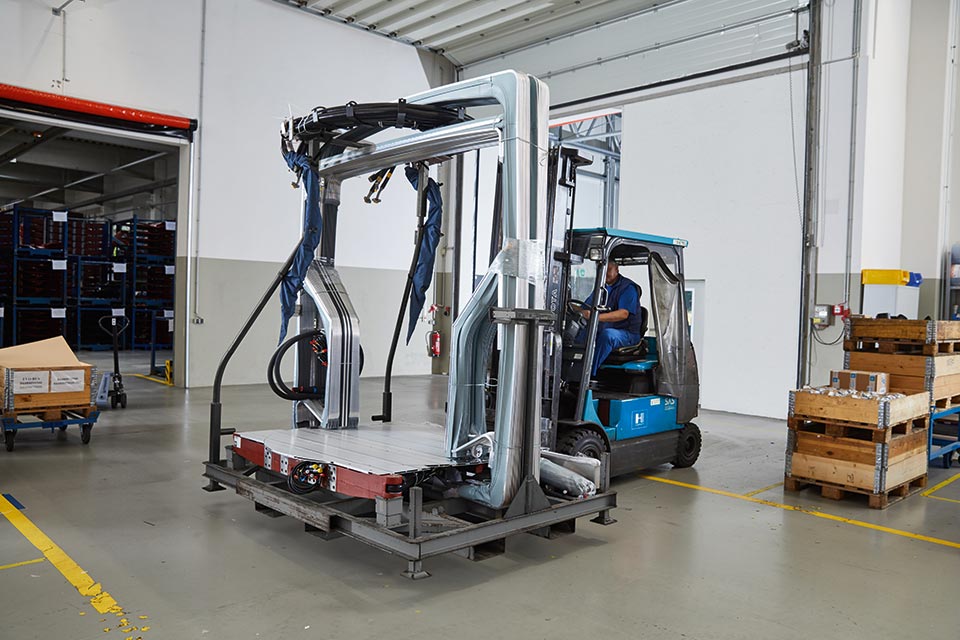
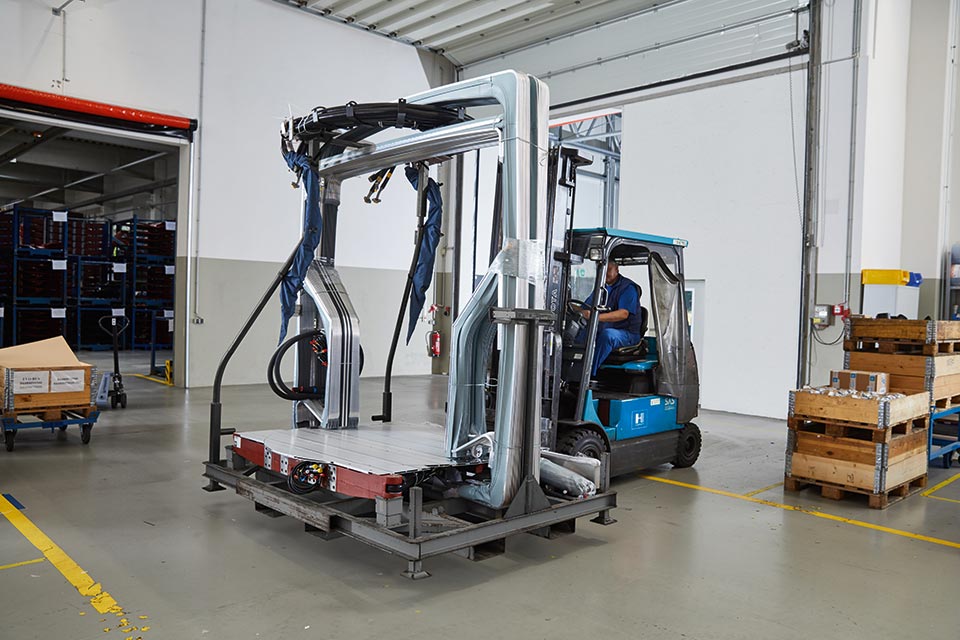
Produktübersicht
Bustechnik und der Name HÜBNER sind seit langer Zeit erfolgreich miteinander verbunden. Den ersten Faltenbälgen für Gelenkbusse im Jahr 1952 ließ das Unternehmen immer wieder wegweisende Neuerungen folgen, unter anderem das erste Niederflurgelenk in Serienfertigung, das erste redundante Gelenkdämpfungssystem und in jüngster Vergangenheit die neue Gelenkfamilie HNGK 19.5, die sich durch eine besonders leichte, gewichtsparende Konstruktion auszeichnet, sowie die weltweit ersten halogenfreien Faltenbälge.
Die unternehmenseigenen Abteilungen für Forschung und Entwicklung arbeiten ständig an Verbesserungen, unter anderem an innovativen Faltenbalgstoffen. Erprobt werden auch Materialien mit optimiertem Brandschutz und höherer Umweltverträglichkeit. Partnerschaften mit wissenschaftlichen Instituten sorgen für weiteren Wissenstransfer und die Einbindung der neuesten technologischen Entwicklungen.
Downloads
Entdecken Sie unsere vielfältige Produktpalette für Busse
Bustechnik und der Name HÜBNER sind seit langer Zeit erfolgreich miteinander verbunden. Den ersten Faltenbälgen für Gelenkbusse im Jahr 1952 ließ das Unternehmen immer wieder wegweisende Neuerungen folgen, unter anderem das erste Niederflurgelenk in Serienfertigung, das erste redundante Gelenkdämpfungssystem und in jüngster Vergangenheit die neue Gelenkfamilie HNGK 19.5, die sich durch eine besonders leichte, gewichtsparende Konstruktion auszeichnet, sowie die weltweit ersten halogenfreien Faltenbälge.
Die unternehmenseigenen Abteilungen für Forschung und Entwicklung arbeiten ständig an Verbesserungen, unter anderem an innovativen Faltenbalgstoffen. Erprobt werden auch Materialien mit optimiertem Brandschutz und höherer Umweltverträglichkeit. Partnerschaften mit wissenschaftlichen Instituten sorgen für weiteren Wissenstransfer und die Einbindung der neuesten technologischen Entwicklungen.
Produktübersicht
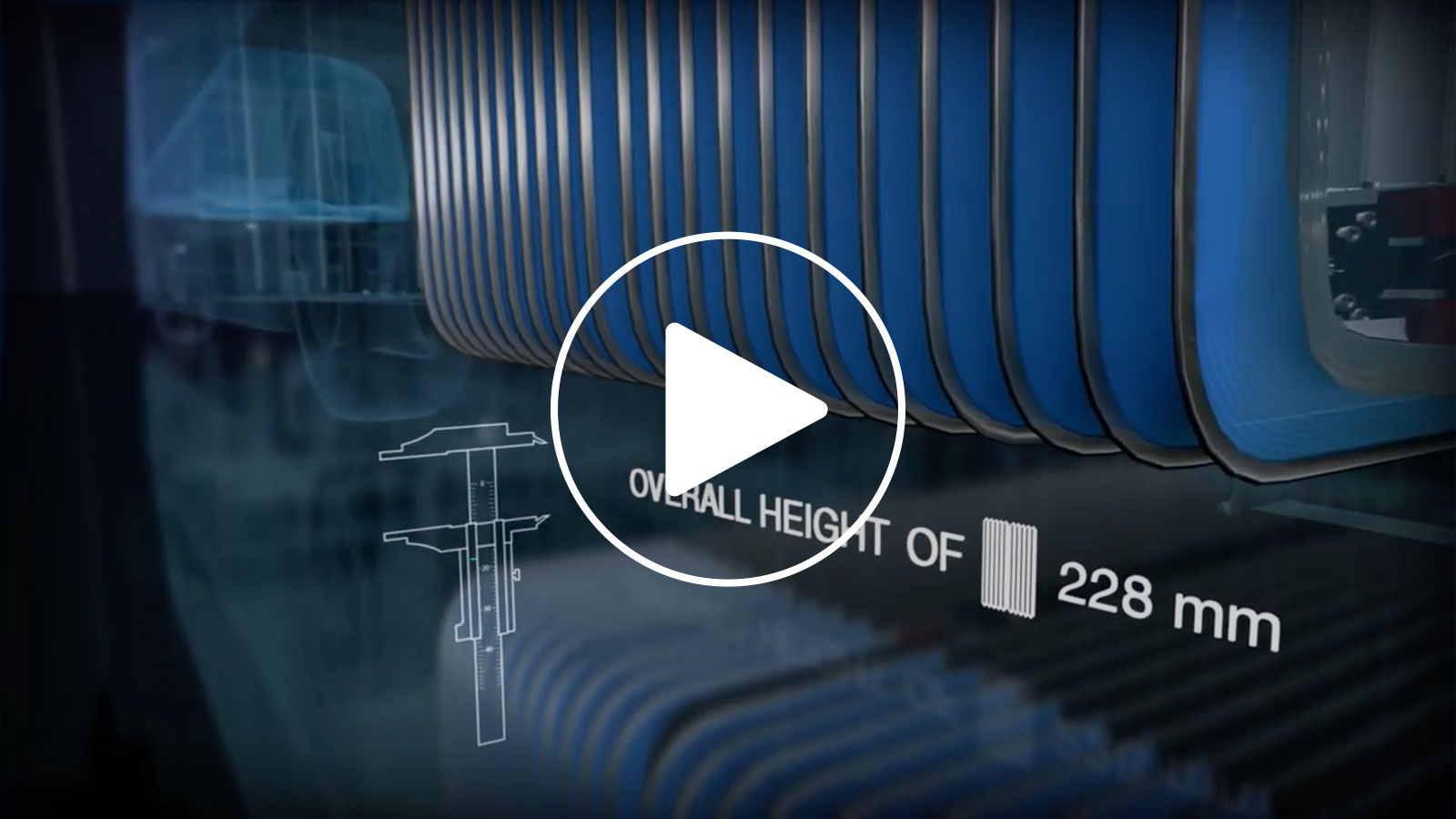
Please click previewimage to start video (privacy-policy).
Die Weiterentwicklungen dienen immer dem Kunden – oder deren Kunden. Etwa bei der Farbgestaltung: So lassen sich Fahrzeugübergänge nun optisch stärker ins Gesamtdesign der verbundenen Wagen integrieren. Ein neuer Trend sind lichtdurchlässige Balgmaterialien. Sie leiten das Tageslicht in die Wagenübergänge und schaffen so ein neues, freundliches Raumgefühl.
Komfort und Sicherheit im Einstiegsbereich
Auch im Bereich Türsicherheit ist HÜBNER ein verlässlicher Partner: Seit dem Jahr 2019 gehört GWU zum Unternehmen. Gemeinsam nimmt die Gruppe eine starke Position in der Busbranche ein – sie ist führend im Bereich Türsicherheitsdichtsysteme für den gesamten Mobilitätsbereich. Besondere Highlights des Lieferprogramms sind innovative Einklemm-Schutzsysteme. Das Unternehmen hat unter anderem Fingerschutzprofile mit Lichtgittern als berührungsloses Sicherheitssystem entwickelt.
Für mobilitätseingeschränkte Menschen fertigt die HÜBNER Transportation GmbH maßgeschneiderte und bedienungsfreundliche Rampen und Lifte. Die Bus-Einstiegssysteme bauen Barrieren ab und erfüllen höchste Sicherheits- und Qualitätsansprüche.
Die Weiterentwicklungen dienen immer dem Kunden – oder deren Kunden. Etwa bei der Farbgestaltung: So lassen sich Fahrzeugübergänge nun optisch stärker ins Gesamtdesign der verbundenen Wagen integrieren. Ein neuer Trend sind lichtdurchlässige Balgmaterialien. Sie leiten das Tageslicht in die Wagenübergänge und schaffen so ein neues, freundliches Raumgefühl.
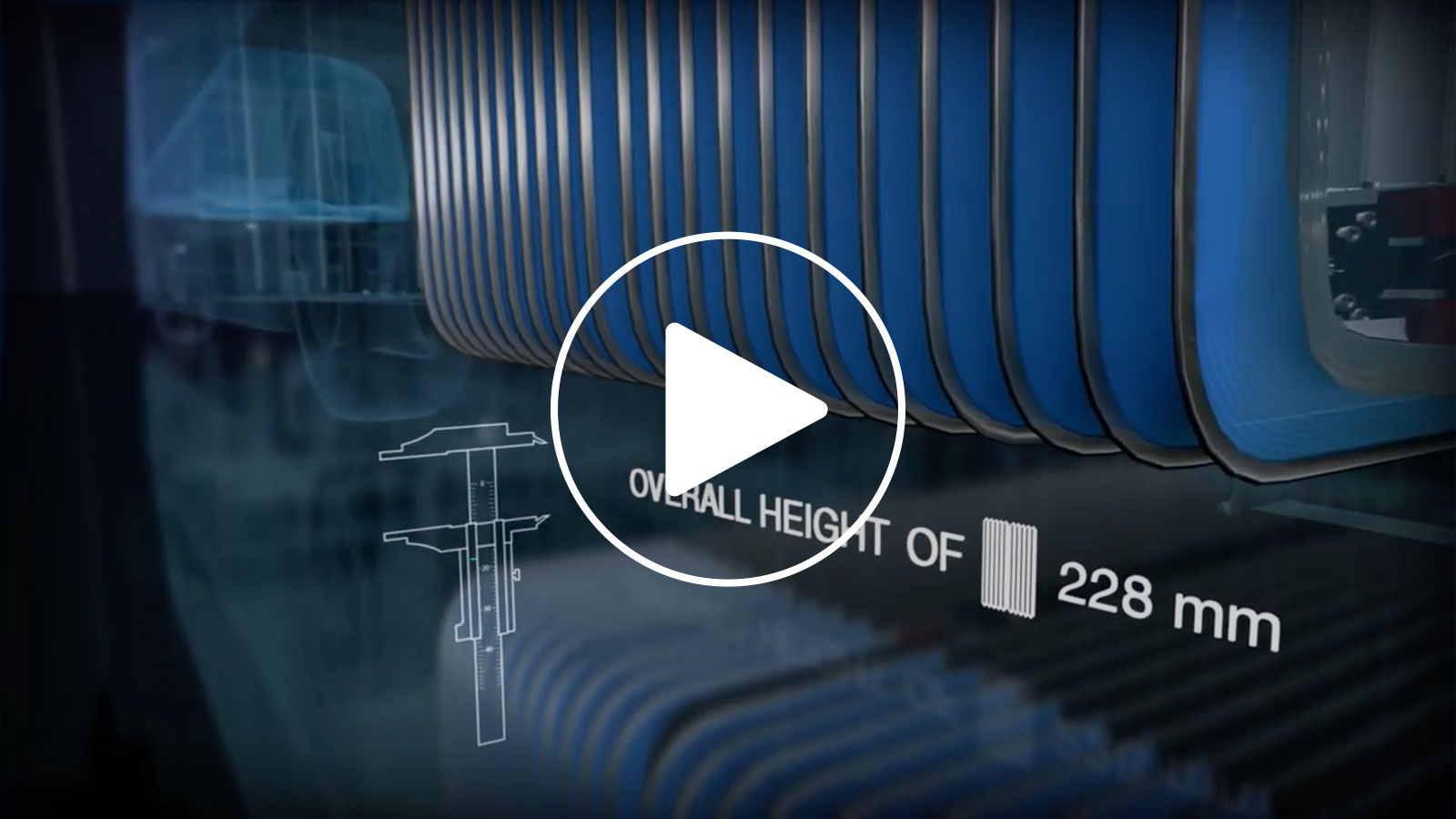
Please click previewimage to start video (privacy-policy).
Komfort und Sicherheit im Einstiegsbereich
Auch im Bereich Türsicherheit ist HÜBNER ein verlässlicher Partner: Seit dem Jahr 2019 gehört GWU zum Unternehmen. Gemeinsam nimmt die Gruppe eine starke Position in der Busbranche ein – sie ist führend im Bereich Türsicherheitsdichtsysteme für den gesamten Mobilitätsbereich. Besondere Highlights des Lieferprogramms sind innovative Einklemm-Schutzsysteme. Das Unternehmen hat unter anderem Fingerschutzprofile mit Lichtgittern als berührungsloses Sicherheitssystem entwickelt.
Für mobilitätseingeschränkte Menschen fertigt die HÜBNER Transportation GmbH maßgeschneiderte und bedienungsfreundliche Rampen und Lifte. Die Bus-Einstiegssysteme bauen Barrieren ab und erfüllen höchste Sicherheits- und Qualitätsansprüche.
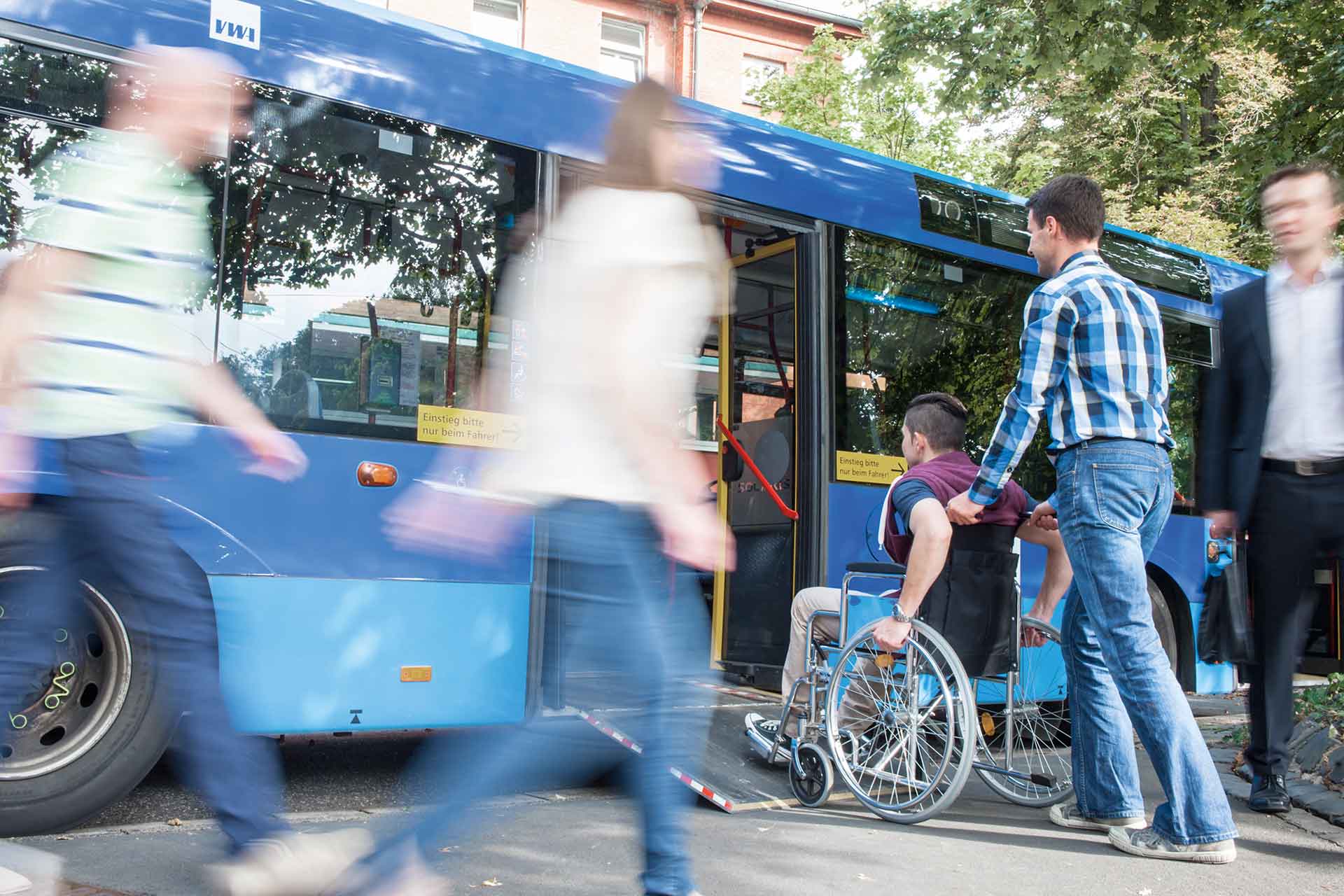
Elektrisch bewegt
Elektromobilität ist nicht nur im Individualverkehr ein Trend. Auch immer mehr Busse fahren mit elektrischem Antrieb und schonen so Klima und Ressourcen. HÜBNER unterstützt die Entwicklung. Hierzu hat das Unternehmen seine innovativen Energieführungssysteme für unterschiedliche Gelenkbustypen um ein Paket für E-, Hybrid- und Trolleybusse erweitert. Damit die Energie zuverlässig genau dort ankommt, wo das Fahrzeug sie braucht.