For the whole
product life cycle
HÜBNER produces high-performance systems that are exceedingly reliable. But the benefits customers receive do not end simply with the delivery of a superior product. HÜBNER supports its customers throughout the entire product life cycle with its comprehensive know-how and experience.
HÜBNER's range of services:
- Full service: Spare parts and maintenance contracts
- Initial installation: Installation training and warranty extension
- Utilization phase: Checks and training
- Maintenance phase: Fast service and outstanding spare parts management
- Servicing strategy: Smart planning, repair and analysis
- Midlife overhauls & refurbishment: Cost-efficient overhauls
- End-of-life service: Environmentally sound disposal
HÜBNER sees these services as an important responsibility and therefore has created a dedicated organizational unit to handle them – the new After Sales & Service segment. In this unit, the relevant competencies from sales, project management, design, technical services and repairs have been brought together. The experienced and highly effective team that has been created is there to concentrate entirely on the after sales and service needs of HÜBNER customers. Without lengthy waiting times.
In each phase of the product life cycle, our aim is to provide maximum customer benefit. It is our goal to minimize downtimes and costs for transport operators and to increase the profitability of vehicles in operation. HÜBNER experts work closely together with the involved specialists from our customers to achieve this.
Your Digital Service Portal – HUBLink
With HUBLink, we offer a digital platform that optimally supports transportation operators in the operation and maintenance of their vehicle fleets. The portal provides targeted information and services for HÜBNER products, making life-cycle costs (LCC) transparent. This way, you know exactly when components need to be replaced or renewed.
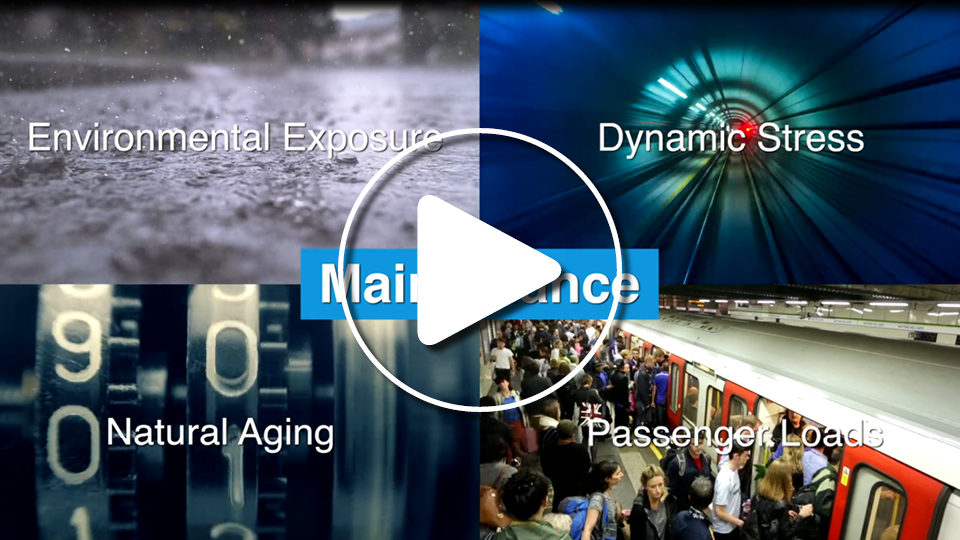
Please click previewimage to start video (privacy-policy).
After Sales & Service
for rail gangways
Typically railway vehicles have an operating life of 30 to 40 years. The gangway systems of the vehicles, however, have a shorter life cycle because they are one of the vehicle components that is subject to the highest stress levels. During every kilometer of travel gangways are compensating for the different motions between the cars.
Particularly in curves, enormous forces are exerted on the folding or corrugated bellows and the other elements of the gangways. Exposure to weather conditions also cause the flexible connections to age more quickly than components that are not directly exposed to the outside environment. Depending on the routes that are traveled, climate factors, operating hours and the quality of maintenance, gangways on average need to be replaced or refurbished every 12 to 15 years.
It is unavoidable that gangways will have to be replaced – at the latest at some point in the middle of a railway vehicle's overall life cycle. With the right planning, however, the costs of this necessary step can be reduced considerably.
Our full-service support for you
To ensure maximum availability of your fleet, HÜBNER offers full-service support on a customer and project-specific basis – with annual contracts or for the complete project life cycle.
Spare part and maintenance contracts
We can handle the stocking and delivery of agreed spare parts as well as maintenance and repair services – in agreements tailored to your specific wishes and requirements.
Retrofitting with HÜBNER gangways
You're not satisfied with the performance of third-party products or would like to implement new gangways in an existing railway vehicle? We will be pleased to provide assistance: With our HÜBNER Motion Recording technology, it is possible to measure and record the relative movements of the railway carriage bodies to one another – for an entire rail route. Using special sensors all the positions of the carriage bodies to one another are recorded in all situations along the route. The measurement system determines the actual relative vehicle movements and provides a picture of the real levels of stress that can be expected for the gangway system when in actual operation.
Based on these data and state-of-the-art 3D measurement sensors, we can quickly and efficiently develop alternative systems. We also use an analysis of the converted measurement data to prepare an endurance testing program and subsequent validation of the HÜBNER solution. The only gangways we deliver are ones that can then be used safely and efficiently in long-term operation.
Service at GERSYS
The HÜBNER company GERSYS has a highly flexible and expert in-house service center to handle all customer needs. Not only can GERSYS devices be repaired well beyond planned product life cycles, service is also available for third-party devices. Customers benefit in many ways:
- Long-term stocking and supply of spare parts and substitute devices
- Device support of at least 15 years, also after termination of a particular model cycle
- Highly durable components and 2nd-source strategy
- Regular obsolescence checking and last-time buying information for contract customers
- For later replacement requirements, devices compatible in form, fit and function are made avilable to avoid cost-intensive software changes and registration processes.
Find out more about GERSYS products
Maximilian Schäfer
Head of Sales
BU Gangways HKS | Mobility Rail
Tel. +49 561 998 1679
Maximilian.Schaefer(@)hubner-group.com